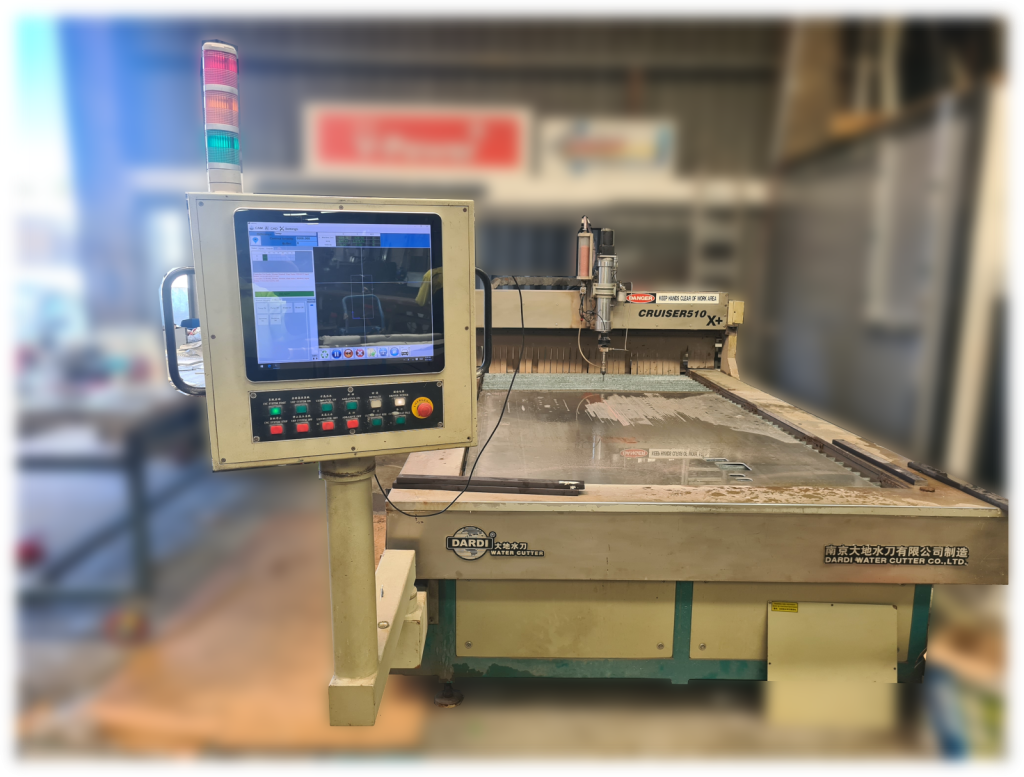
Dardi is among the leading Chinese brands of Waterjet cutters. However, when the original Fagor controller on this particular refused to power up, MDSmotion was called in to the rescue.
Retrofit Details:
- Machine Configuration:
- Servo X, Y (Yaskawa)
- Z Axis driven by DC Motor
- 4 x Digital Outputs required
- 5 x Digital Inputs required (including limits for X and Y)
- Key Control Equipment supplied by MDSmotion:
- 1 x G2-M104A Motion Controller
- 1 x ISOIO-0808 Relay Boards
- 1 x MDSnc PC Software
- 1 x AIOPC Industrial 17″ Panel PC
- Control Methodology:
- X and Y Axis Drives (Yaskawa) running in Velocity Mode and commanded by +/- 10V analog signal from G2-M104A. Position feedback via Quadrature Incremental Encoder.
- X and Y uses physical limit switches for homing.
- Relay outputs from 4 of the ISOIO-0808 boards are used to control various operations of the machine, such as pumps, pneumatic valves, motors etc.
- Isolated inputs from the ISOIO-0808 boards are used to interface with sensors and push buttons on the machine.
Since the control software now uses MDSmotion’s MDSnc, the machine is much easier to operate. Not only that, but since MDSnc can open DXF files directly and create tool paths itself, there is no need for 3rd party post processors. CAD design can either be done directly from within MDSnc, or by using a dedicated CAD software such as AutoCAD or DoubleCAD XT (available for free).